Avoid Costly Downtime: How to Effectively Troubleshoot Industrial Machinery
Industrial machinery plays a crucial role in the manufacturing sector, enabling efficient production and ensuring smooth operations. However, when breakdowns occur, they can lead to costly downtime and production delays. To minimize these setbacks, it is essential for businesses to have an effective troubleshooting guide in place. In this article, we will explore the key steps involved in troubleshooting industrial machinery and provide valuable tips to help you get your operations back up and running in no time.
Understanding the Importance of Troubleshooting
Before delving into the actual troubleshooting process, it is important to recognize why troubleshooting is crucial for industrial machinery. Troubleshooting allows businesses to identify and address issues promptly before they escalate into major problems. By doing so, companies can prevent unexpected breakdowns that could result in significant financial losses due to halted production or expensive repairs.
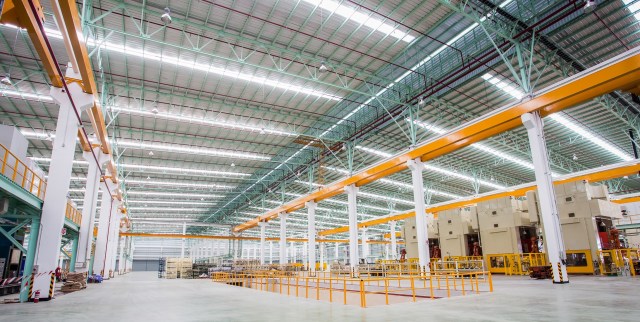
Step 1: Gather Information and Assess Symptoms
The first step in effectively troubleshooting industrial machinery is gathering as much information as possible about the issue at hand. This involves talking with machine operators or maintenance personnel who may have noticed any unusual behavior or symptoms leading up to the problem. Ask detailed questions about specific noises, warning lights, error messages, or any other abnormal indications that could help identify potential causes.
Once you have gathered information from those on-site, visually inspect the machinery yourself. Check for loose connections, damaged parts, or any signs of wear and tear that may be contributing factors. Take note of any visible issues that could be causing the problem.
Step 2: Analyze Potential Causes
After gathering information and assessing symptoms, it’s time to analyze potential causes of the problem. Start by referring to the manufacturer’s manual for guidance on common issues related to your specific industrial machinery model. Often, these manuals contain troubleshooting charts or flowcharts that can help you narrow down possible causes based on observed symptoms.
If the manufacturer’s manual doesn’t provide sufficient guidance, consult with experienced technicians or industry experts who may have encountered similar problems before. Their expertise can be invaluable in identifying potential causes that may not be immediately apparent.
Step 3: Implement a Systematic Approach
Once you have identified potential causes, it is important to implement a systematic approach to troubleshoot industrial machinery effectively. Start by ruling out the simplest and most common causes first. Check for loose connections, faulty wiring, or any other issues that are relatively easy to resolve.
If the problem persists, move on to more complex troubleshooting steps. This may involve using specialized tools such as multimeters or diagnostic software to pinpoint electrical or mechanical malfunctions accurately. Follow the manufacturer’s recommended procedures for testing and inspecting specific components or subsystems.
Step 4: Take Appropriate Actions
After identifying the root cause of the problem, it’s time to take appropriate actions to resolve the issue and prevent future occurrences. This may involve repairing or replacing faulty parts, recalibrating sensors, updating software/firmware if applicable, or implementing preventive maintenance measures.
Document all actions taken during the troubleshooting process and keep records of repairs made. These records will prove valuable when analyzing historical data for recurring issues and developing proactive maintenance plans in the future.
By following these steps and regularly updating your troubleshooting guide based on new insights gained from experience, you can significantly reduce costly downtime caused by industrial machinery breakdowns and ensure smooth operations within your manufacturing facility.
In conclusion, effective troubleshooting of industrial machinery is essential for minimizing downtime and maintaining efficient production processes. By understanding the importance of troubleshooting, gathering information about symptoms, analyzing potential causes systematically, and taking appropriate actions promptly, businesses can prevent unexpected breakdowns and optimize their overall productivity. Remember to continuously improve your troubleshooting guide based on lessons learned from past experiences for long-term success in troubleshooting industrial machinery effectively.
This text was generated using a large language model, and select text has been reviewed and moderated for purposes such as readability.